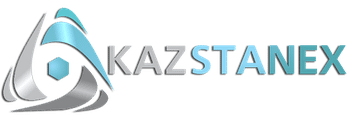
Обрабатывающий центр серия nest concept max

Доставка
Оплата
Описание
Обрабатывающий центр Серия NEST concept MAX
Данная автоматическая производственная линия предназначена для скоростного высококачественного смешанного раскроя полноформатных плитных материалов (ДСП, МДФ) посредством фрезерования с последующей присадкой технологических отверстий по технологии «NESTING».
ОБЛАСТЬ ПРИМЕНЕНИЯ:
Древесина любых пород, композитные материалы (ДСП, ДВП, МДФ, фанера и т. д.), «Dibond», «Alucobond», любые полистиролы (в том числе ПВХ и полистиролы с поликарбонатом), гетинакс, искусственный камень, акриловое стекло и оргстекло, модельный пластик и т. п.
СХЕМЫ ОБРАБОТКИ:
ОТЛИЧИТЕЛЬНЫЕ ОСОБЕННОСТИ:
В последние годы все больше отечественных предприятий приобретают обрабатывающие центры для работы по технологии «NESTING». Действительно, данная технология имеет ряд преимуществ. В классическом варианте процесса производства мебели плитный материал сначала обрабатывается на форматно-раскроечном оборудовании, затем на сверлильно-присадочном, тогда как при технологии «NESTING»:
- Раскрой и сверление проводятся на одном станке за один проход. За счет меньшего количества рабочих операций существенно сокращается время изготовления деталей и дополнительные издержки на транспорт и хранение. К тому же оптимизация раскроя широкоформатных плит позволяет экономить сырье. Расположение деталей относительно друг друга на одном листе имеет большое значение, особенно при производстве деталей разной формы. Исчезает необходимость предварительно раскраивать лист на полосы, а при изготовлении деталей сложной формы не обязательно раскраивать лист на прямоугольные заготовки.
- Отсутствие человеческого фактора в данном случае положительно влияет на точность и качество выполняемых операций, вероятность погрешности и ошибки станка очень мала.
- При использовании технологии «NESTING»сокращается срок изготовления комплекта мебели, существенно увеличивая производительность предприятия.
- Использование технологии «NESTING»позволяет сократить персонал и существенно повысить рентабельность предприятия.
Конечно, целесообразность и эффективность использования технологии «NESTING» зависит от специфики конкретного производства. Определяющими факторами выбора оборудования для технологии «NESTING» или традиционного производства будут являться производимое количество изделий, их серийность или индивидуальность, необходимость оптимизации раскроя и гибкого производственного процесса. Данные станки представляют интерес как для производителей лестниц, окон, дверей, кухонной мебели, где требуется обработка фасадов сложных форм, так и для компаний, занимающихся изготовлением фигурных декоративных изделий из пластмассы, легкого металла, композитных материалов из алюминия, например, алюкобонда или массивной древесины.
На сегодняшний день станкостроительные компании предлагают достаточно широкий выбор оборудования для работы по технологии «NESTING» различного уровня сложности и технических возможностей и соответственно стоимости. Beaver предлагает самое доступное решение по применению данной технологии на мебельном производстве выпустив серийную автоматическую линию с ЧПУ для работы по данной технологии Beaver NEST concept.
Основу конструкции линии составляет мощный портальный обрабатывающий центр, скорости перемещения на котором могут достигать до 80 м/мин.
На эффективность использования технологии «NESTING» влияют конкретные условия работы мебельного производства. Так, технология может успешно применяться на мелких и средних предприятиях, которым нецелесообразно иметь на своем производстве многочисленный машинный парк. Для крупных предприятий подобное оборудование выгодно отличается высокой производительностью при большом объеме выпуска разнообразной продукции. Технология «NESTING» может использоваться при сложной фрезерной обработке деталей. Это обусловлено в первую очередь возможностью проведения большого числа операций на одном обрабатывающем центре с получением готовой детали и увеличением полезной площади заготовок. Незаменима данная технология и при воплощении сложных дизайнерских проектов, при работе с заготовками сложной непрямоугольной формы.
КОНСТРУКТИВНЫЕ ОСОБЕННОСТИ:
УСИЛЕННАЯ ЦЕЛЬНОСВАРНАЯ МАССИВНАЯ СТАЛЬНАЯ СТАНИНА
Выполнена из толстостенных стальных труб прямоугольного сечения толщиной 8 - 12 мм, что обеспечивает высокую степень жесткости конструкции станка, устойчивость к статическим и динамическим нагрузкам, поглощает вибрацию при работе. Высокая геометрическая точность фрезерованных площадок под направляющие достигается за счет технологической возможности обработки станин за одну установку на металлообрабатывающих центрах с ЧПУ. Это дает возможность получить гарантированно высокую точность и качество при обработке заготовок любых размеров.
МАССИВНЫЙ СТАЛЬНОЙ ПОРТАЛ
Изготовлен из толстостенных стальных труб прямоугольного сечения толщиной 10 мм (усиленных до 20 мм в местах сопряжений), что обеспечивает высокую степень жесткости портала станка, устойчивость к статическим и динамическим нагрузкам. Высокая геометрическая точность фрезерованных площадок под направляющие достигается за счет технологической возможности обработки порталов за одну установку на металлообрабатывающих центрах с ЧПУ.
Данная конструкция позволяет получить гарантированно высокую точность и качество при обработке заготовок практически из любых материалов на предельно возможных максимальных скоростях обработки.
УСИЛЕННАЯ КОНСТРУКЦИЯ ОПОР ПОРТАЛА
Портал установлен на массивные опоры, увеличивающие жесткость конструкции портала, а также повышающие устойчивость к деформациям. Увеличенная базовая опорная площадка имеет «Т» образную форму с шестью крепежными отверстиям, что позволяет значительно увеличить нагрузочные показатели станка, без потери качества обработки.
ВЫСОКОТОЧНЫЕ ЛИНЕЙНЫЕ НАПРАВЛЯЮЩИЕ ПОВЫШЕННОЙ ЖЕСТКОСТИ «tdK» (ЯПОНИЯ)
За счет повышенной устойчивости и жесткости обеспечивают высокую точность перемещения портала, суппорта и высокооборотного шпинделя по осям X, Y и Z. Достигается высокая точность обработки и долговечность работы станка без потери точностных параметров.
Станки beaver - единственные станки для деревообработки, на которые устанавливаются направляющие premium класса «tdK».
СИСТЕМА ЗАЩИТЫ НАПРАВЛЯЮЩИХ «tdK-LACS» (ЯПОНИЯ) В КОМПЛЕКТЕ С КАРТРИДЖНОЙ СМАЗКОЙ QZ
Контактный скребок LaCS обеспечивает усиленную защиту направляющих и подшипников по всем осям перемещения, а самосмазывающиеся подшипник QZ способны проработать до 5000 км без обслуживания. Данная система позволяет значительно снизить время на обслуживание станка и риск повреждения направляющих за счет недостаточного или избыточного количества смазочного материала. Превосходная защита от пыли, особенно в производстве мебели и деревообработке.
КОЖУХИ ДЛЯ ЗАЩИТЫ НАПРАВЛЯЮЩИХ
Имеют специальный форму и изгиб предотвращающий попадание обрезков и пыли на направляющие и косозубые рейки в процессе работы станка.
КОСОЗУБЫЕ ПЕРЕДАЧИ ШЕСТЕРНЯ – РЕЙКА ПО ОСЯМ X –Y «WMH-Herion» (ГЕРМАНИЯ)
В отличие от передач с прямыми зубьями, косые входят в зацепление постепенно, а не сразу по всей длине. Косозубое зацепление не имеет зоны однопарного зацепления. В прямозубой передаче нагрузки на зубья прикладывается мгновенно. Зубья в косозубых передачах нагружаются постепенно по мере захода их в зону зацепления, в зацеплении всегда находится как минимум две пары зубьев.
Данные факторы определяют плавность работы косозубого зацепления, а также снижение шума и дополнительных динамических нагрузок по сравнению с прямозубым зацеплением. Использование косозубых передач в конструкциях фрезерных станков с ЧПУ Beaver позволило значительно повысить нагрузочные характеристики и увеличить скоростные показатели.
ВЫСОКОПРЕЦИЗИОННАЯ ШАРИКО-ВИНТОВАЯ ПЕРЕДАЧА «PMI» (ТАЙВАНЬ)
За счет исключения люфта обеспечивается высокоточное перемещение шпиндельной площадки по оси Z, а применение шарико-винтовой пары увеличенного сечения гарантирует сохранение точности при выполнении высокоскоростной обработки сложных изделий.
УСИЛЕННАЯ КОНСТРУКЦИЯ ШПИНДЕЛЬНОЙ ПЛОЩАДКИ
В целях снижения уровня вибраций во время обработки проведена модернизация шпиндельной площадки. Увеличено сечение литой конструкции, добавлены дополнительные ребра жесткости, а также установлены усиленные направляющие и ШВП. Данная модернизация повысила скоростные характеристики особенно во время обработки сверлильно-присадочной головой.
ПЛАНЕТАРНЫЕ РЕДУКТОРЫ «SHIMPO-NIDEC» (ЯПОНИЯ) ПО ОСЯМ X, Y
Изменение конструкции узла передачи крутящего момента с ременной передачи на планетарные редукторы «SHIMPO-NIDEC» позволили значительно улучшить показатели оборудования, а именно:
- Реализовать большие удельные мощности при обеспечении высокой нагрузочной способности и минимальных габаритах привода;
- Получить гораздо более высокий КПД;
- Облегчить конструкцию, т.к. данные редукторы вдвое компактней и в три раза легче редукторов других типов, имеющих аналогичные характеристики;
- Уменьшить время на техническое обслуживание оборудования, т.к. данные редукторы не требуют обслуживания и настройки в течение всего срока эксплуатации.
СЕРВОДВИГАТЕЛИ «YASKAWA» (ЯПОНИЯ)
Установленные на каждом узле для перемещения по осям X, Y и Z, обеспечивают высокоточное позиционирование шпинделя (до 0,001 мм) в соответствии с заданной программой при высокой скорости перемещения до 80 м/мин. Данные серводвигатели хорошо зарекомендовали себя высокой степенью надежности и стабильности даже при работе в тяжелых производственных условиях. Данный тип серводвигателей используется на высокоскоростных станках тяжелой серии, в том числе и на пяти осевом оборудовании.
ВСПОМОГАТЕЛЬНЫЙ РОЛИКОВЫЙ СТОЛ
Для предотвращения повреждения декоративного покрытия листового материала во время загрузки в рабочую зону станка установлен специальный роликовый стол, по которому происходит перемещение листа.
ВАКУУМНЫЙ РАБОЧИЙ СТОЛ
Вакуумный стол изготавливается из цельных листов упрочненного гетинакса (специального композитного материала на основе фенольных смол и синтетических волокон). В данной конструкции отсутствуют какие-либо переклейки, что гарантирует стабильность работы вакуумного стола на протяжении всего срока службы оборудования.
Применение минимального шага ячейки и большого количества вакуумных каналов (252 отверстия) позволяют сохранить высокую эффективности вакуумного прижима. Для удобства обработки мелких деталей или обработки разных форматов листов, вся поверхность рабочего стола поделена на 7 зон. Комбинация разных зон будет соответствовать стандартам панели:
1 + 2 + 3 + 4 = формат 1220 x 2440 мм
1 + 2 + 3 + 4 + 5 + 6 = формат 2800 x 2070 мм
1 + 2 + 3 + 4 + 5 + 7 = формат 1500 x 3000 мм
ПНЕВМАТИЧЕСКИЕ БАЗИРУЮЩИЕ УПОРЫ
Предназначены для базирования заготовок. Упоры установлены спереди, в левой и правой части рабочего стола. По команде управления упоры поднимаются для базировки заготовки, после чего заготовка фиксируется при помощи вакуума, а упоры опускаются, не препятствуя обработке.
ТАРЕЛЬЧАТЫЙ МАГАЗИН АВТОМАТИЧЕСКОЙ СМЕНЫ ИНСТРУМЕНТА
Система автоматической смены инструмента с тарельчатым магазином на 8 позиций. Данная система, в отличие от линейной системы смены инструмента располагается непосредственно на портале станка, что обеспечивает быстроту смены инструмента в среднем на 50% быстрее, чем при использовании линейного.
ДАТЧИК АВТОМАТИЧЕСКОГО ИЗМЕРЕНИЯ И КАЛИБРОВКИ ДЛИНЫ ИНСТРУМЕНТА
Обеспечивает существенную экономию времени и уменьшение времени простоя станка за счет:
- высокой точности измерения длины инструмента;
- автоматизации расчета и ввода коррекции на инструмент;
Станок производит калибровку полностью в автоматическом режиме, исключая ошибки, связанные с неточными действиями оператора, что в свою очередь способствует снижению брака.
ИНСТРУМЕНТАЛЬНЫЕ ПАТРОНЫ
В комплекте со станком поставляются 3 инструментальных патрона ISO30 или HSK63 (в зависимости от модификации шпинделя).
ШКАФ УПРАВЛЕНИЯ
Шкаф управления - самый основной элемент станка и от его надежности зависит дальнейшая стабильная работа оборудования. Шкаф управления линии оснащен комплектующими ведущих мировых производителей (Delta, Schneider, Omron, Telemecanique, Siemens) и скомпонован в отдельный блок, изолированный от вибраций, перегрева и других внешних воздействий. Все компоненты и соединения расположены на строго отведенных местах и имеют легкий доступ для контроля и обслуживания.
ЯЩИК ДЛЯ ИНСТРУМЕНТА (ЗИП)
Эргономичный инструментальный ящик включающий набор фрез и цанг, смазочный комплект, набор ключей и т.д.
ОБЯЗАТЕЛЬНЫЕ ИСПЫТАНИЯ В ЛАБОРАТОРИИ КОНТРОЛЯ КАЧЕСТВА
Завод-изготовитель гордится своей лабораторией контроля качества обработки, т. к. это является одной из важнейшей составляющей надежности оборудования и долгих лет стабильной работы. Обязательные испытания точности обработки станка происходят с помощью высокоточного измерительного оборудования известного мирового производителя - компании RENISHAW.
Если точность позиционирования станков с ЧПУ соответствует требованиям, то окружность, представляющая траекторию перемещения рабочего органа, будет точно соответствовать запрограммированной круговой траектории. На практике же, радиус реальной окружности отклоняется от радиуса запрограммированной окружности. Таким образом, если бы было возможно точно измерять координаты фактической круговой траектории и сравнивать их с заданной в программе траекторией, то пользователь получил бы критерий оценки технического состояния станка. Именно этот подход лежит в основе работы системы ballbar, которая представляет собой отраслевой стандарт для диагностики технического состояния станков. Сердцем системы является сам датчик ballbar – прецизионный телескопический линейный датчик с высокоточными сферами, установленными с двух сторон. При использовании системы, сферы датчика фиксируются в магнитных держателях с высокой повторяемой точностью базирования. Один из этих держателей крепится на столе станка, а другой – в шпиндель станка или корпус шпинделя. Такая конструкция позволяет с помощью датчика ballbar измерять чрезвычайно малые отклонения радиуса по мере того, как на станке описывается запрограммированная круговая траектория. Полученные данные используются для расчета суммарных показателей точности позиционирования (округлости, отклонения от окружности) в соответствии с такими международными стандартами, как ISO 230- 4 и ASME B5.54, государственного стандарта Российской Федерации ГОСТ 30544—97. Результаты выводятся в графическом и численном виде, что обеспечивает наглядность и удобство в процессе выявления ошибок станка.
На данный момент оборудование «Beaver» является единственным оборудованием с ЧПУ данного класса, при настройке и тестировании которого используется такое диагностическое оборудование.
Технические характеристики: | |||||||||
Размеры вакуумного стола, мм | 2070 x 3000 | ||||||||
Размеры зоны перемещения X и Y, мм | 2100 x 3050 | ||||||||
Макс. высота заготовки по Z, мм | 50 | ||||||||
Тип рабочего стола | вакуумный, матричный на 7 зон | ||||||||
Система смены инструмента | автоматическая | ||||||||
Тип инструментального магазина | тарельчатый на портале | ||||||||
Количество мест в магазине | 8 | ||||||||
Тип датчика калибровки инструмента | автоматический | ||||||||
Тип электродвигателей перемещения | сервопривод | ||||||||
Скорость рабочего хода, м/мин | 0 – 30* | ||||||||
Скорость холостого хода по осям X / Y, м/мин | 0 – 80 | ||||||||
Скорость холостого хода по оси Z, м/мин | 0 – 25 | ||||||||
Давление в пневмосистеме, МPa | 0,6 – 0,7 | ||||||||
Общая установленная мощность, кВт | до 35,0** | ||||||||
Напряжение, В | 380 | ||||||||
Частота тока, Гц | 50 | ||||||||
Габаритные размеры (в упаковке): | |||||||||
Длина, мм | 4900*** | ||||||||
Ширина, мм | 2250*** | ||||||||
Высота, мм | 2000*** | ||||||||
Вес, кг | 4500 |
* Данное значение зависит от множества факторов, таких как обрабатываемый материал, инструмент, глубина фрезерования и т. д.
** В зависимости от выбранной модификации станка
*** Указаны габариты и вес без учета системы загрузки-выгрузки